In the oil & gas industry, Engineers often spend hours performing calculations to design a gas compressor system. In the case of Gas transmission through pipelines, the performance of a gas compressor becomes critical and can decide whether you are going to see gas production coming to a halt or it's just 'Another Day, Another Dollar'. Design methods are initiated by doing 'steady state' calculations, However nothing can be more frustrating for the engineer to watch his/her 'steady state design' ending up conking out the gas compressor once its built, because he/she failed to judge whether the system was under-designed or over-designed.
The worst periods experienced by a gas compression system is during start-up, normal shutdown and emergency shutdown. Other events such as change in production, gas composition variation or discharge valve failure to name a few may or may not be as stressful, but can still produce some of the worst effects on gas compressor operation - namely, Compressor Surge that causes mechanical damage to the gas compressor.
Here are 6 ways that engineers can revisit their design to attend to the dreaded compressor surge scenario that can put the gas plant out of service.
Larger Anti-surge Valve (ASV) Size with a Quick Opening Valve

Points to Remember
- Allows more flow to be recycled back to the suction side and enables moving the compressor operating point away from surge line.
- An upper limit exists when increasing the size of the Anti-surge valve. Beyond a certain size of the ASV, recycle flow to the suction side does not increase, but saturates out.
- Larger ASV/QAV would mean longer opening times that causes slower response to surge and also require installing an electric motor in cases where pneumatic valves struggle to quickly lift the valve stem. - Disadvantage: Increases Cost
Suction and Discharge Pipe Re-Routing
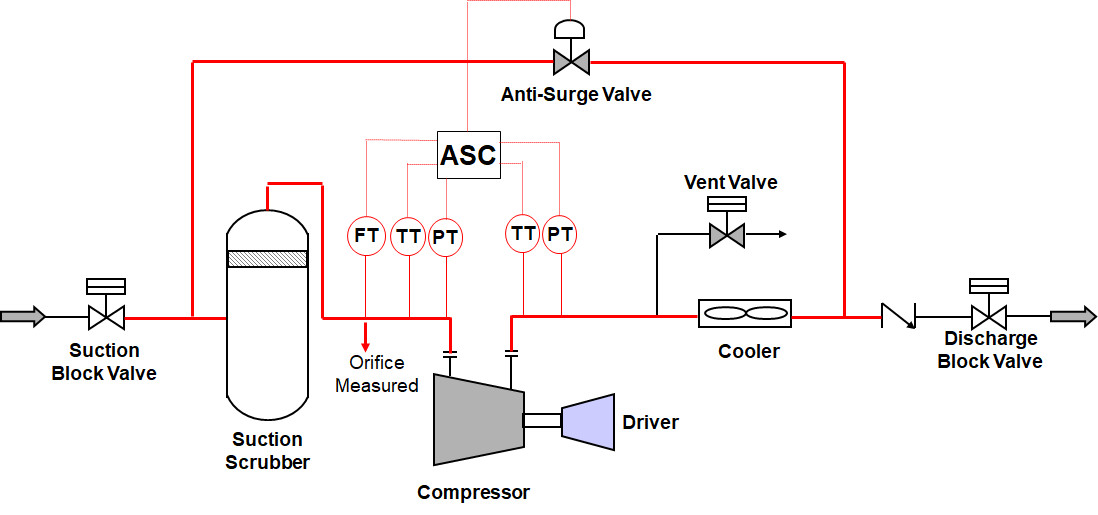
Points to Remember
- Piping Volumes on Suction Side and Discharge Side can be re-routed to minimize time taken by the vapours to recycle back to suction - Shortens the Response Time
- However Piping & Civil Requirements have to be revisited to check for feasibility.
- Larger piping volumes leads to more system inertia and slower response times. Hence over-sizing pipes can be detrimental.
Re-Positioning Anti-surge Tap off- Point
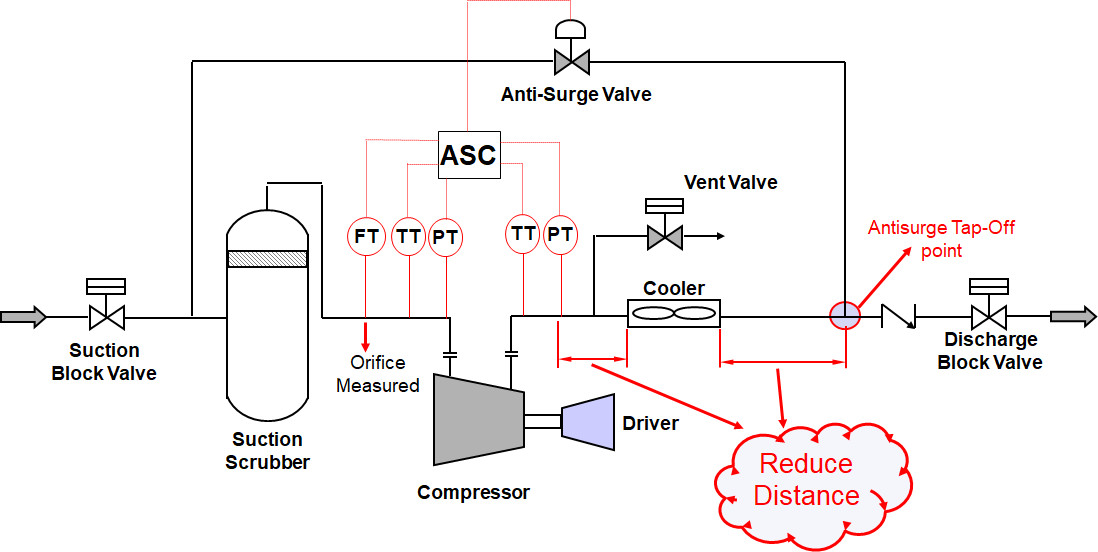
Points to Remember
- Re-positioning the anti-surge tap-off point and cooler Position closer to the compressor discharge reduces the distance required by the discharge gas to recycle to the suction. - Gives shorter response time to surge.
- However moving the tap off points, too close to the compressor discharge can cause vibration problems. Additionally, the anti-surge valve can rattle to exacerbate the failure of pipe supports also.
Slowing Compressor Speed during Coast down
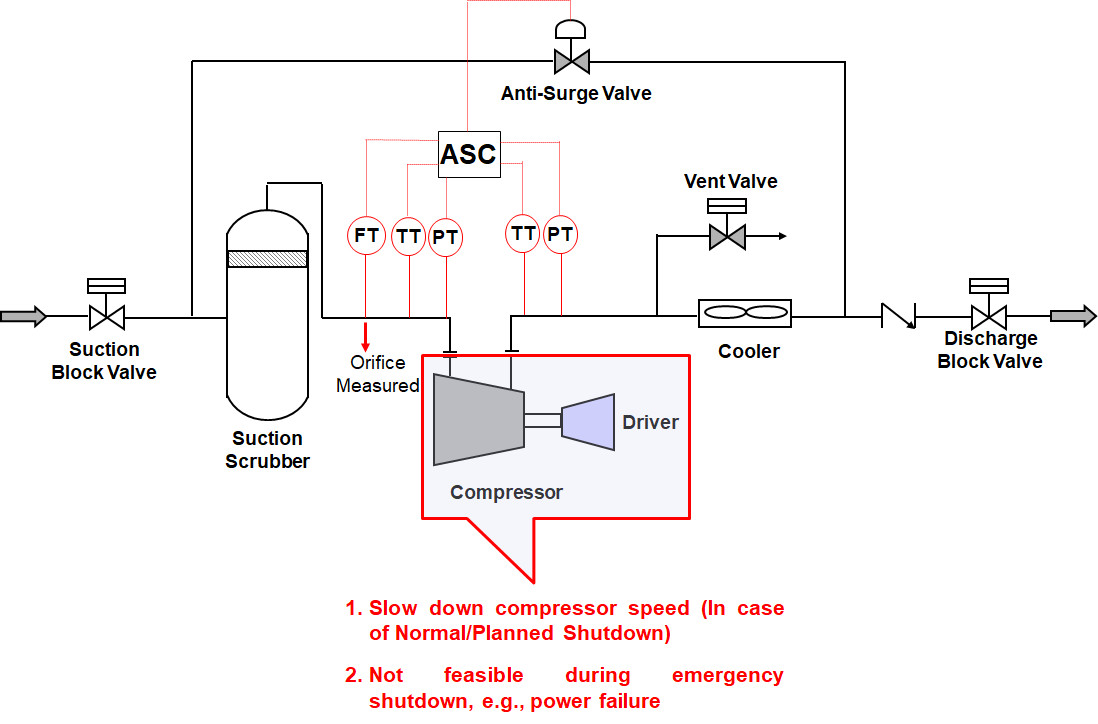
Points to Remember
- This method is feasible for Variable speed drives (VSD) during normal/planned shutdown. Slowing/ramping down the compressor speed gives time for the anti-surge valve to respond and recycle sufficient flow to ensure operating point stays away from the surge line.
- However in case of fixed speed drives, e.g. Asynchronous/synchronous Induction Electric Motors, during an emergency shutdown, no provision exists to control the rate of ramp down. Hence this option has limited applicability.
- Unlike electric motors, gas turbines (GT) continue to run for a short while before speed coasts down to bring the compressor to a grinding halt. This is because, during shutdown, when fuel supply to the GT is cut-off, residual fuel in the supply manifold continues to burn for some time keeping the turbine speed from coasting down immediately. This allows the compressor's anti-surge system (ASC) to buy time to respond sufficiently to keep the operating point away from the surge line.
Discharge Side Gas Flaring
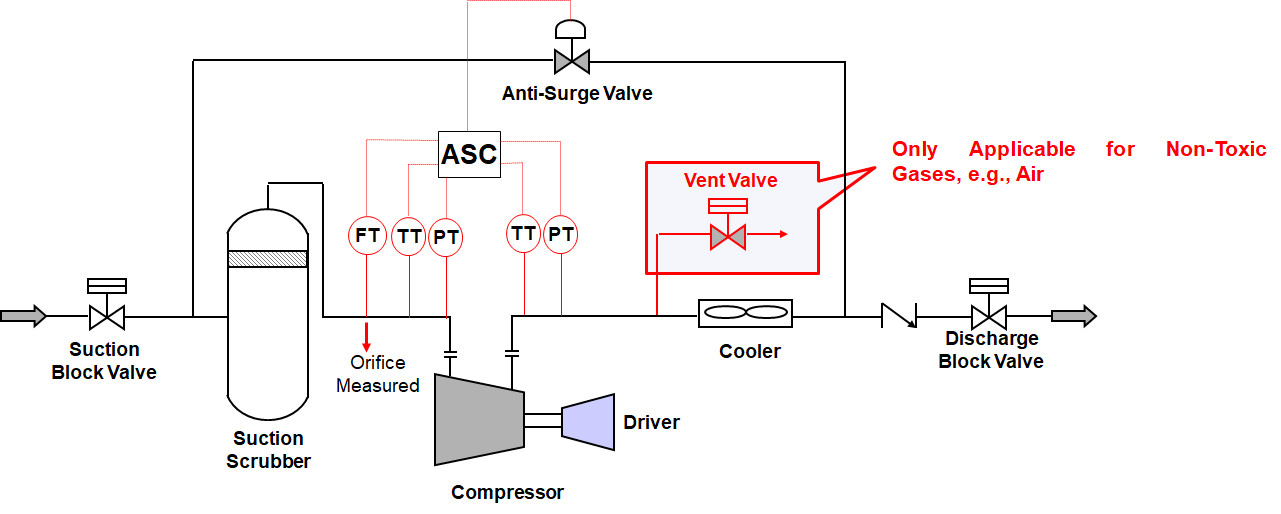
Points to Remember
- Only Applicable for Non-Toxic Gases.
- Used With/Without Anti-surge Line Operation.
- Smaller capacity compressors such as air compressors are sometimes fitted with vent valve without anti-surge line.
- Gas flaring on discharge side is effective to evacuate the discharge side volume of gas quickly thereby reducing system pressure and flow reversal. As a result, operating point can be kept away from the surge line.
Hot Gas Recycle Valve Installation
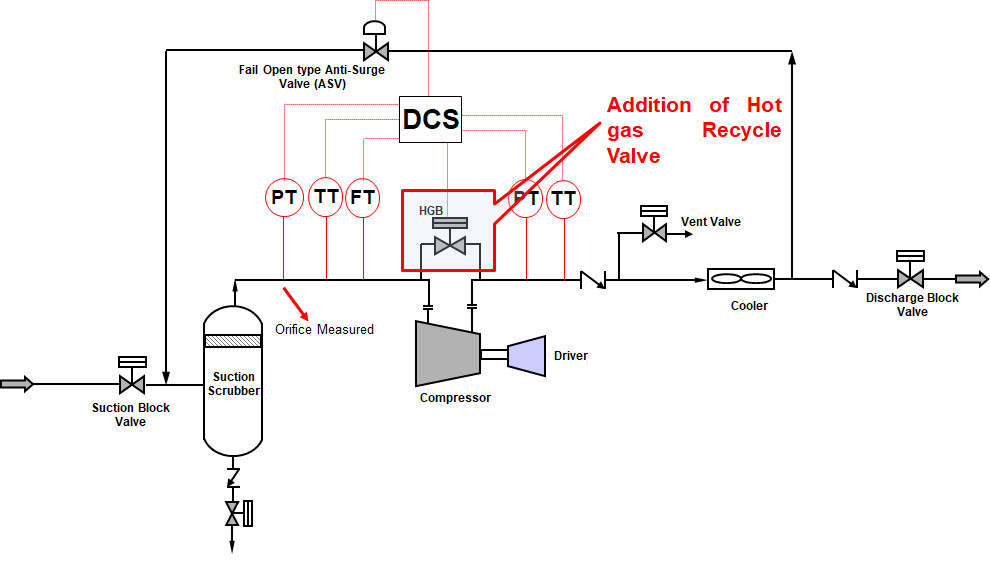
Points to Remember
- To be used as a last resort when all else fails to tackle surge
- The hot gas recycle valve is a quick opening valve with on-off characteristics and operates in fail open mode. It provides the shortest route to recycle hot gas back to the suction side to keep the operating point away from the surge line
- The amount of hot gas recycle flow is to be kept as least as possible to avoid overheating the compressor bearings. Hence vendor participation is also necessary to understand the impact of hot gas recycle method on compressor operation.
Vijay Sarathy holds a Master’s Degree in Chemical Engineering from Birla Institute of Technology & Science (BITS), Pilani, India and is a Chartered Engineer from the Institution of Chemical Engineers, UK. His expertise over 16 years of professional experience covers Front End Engineering, Process Dynamic Simulation and Subsea/Onshore pipeline flow assurance in the Oil and Gas industry. Vijay has worked as an Upstream Process Engineer with major conglomerates of General Electric, ENI Saipem and Shell.