This article is more of a case study on basic design guidelines for parallel gas compressors for pipeline export. The basic equipment required for every gas compression system is
- A suction scrubber that eliminates any liquids & particulate matter that can enter into the gas compressor to cause erosion.
- An air cooler is necessary at the compressor discharge to cool down gas that heats up during compression.
- An anti-surge valve (ASV) or cold recycle line is used to balance pressure on the suction and discharge side of the compressor that prevents a cycling compressor surge conking out the internals.
- A check valve at the compressor discharge flange to prevent any flow reversal in the event of a compressor surge.
Below is a schematic that can give operational problems during startup/shutdown, load variations & air cooler failures.
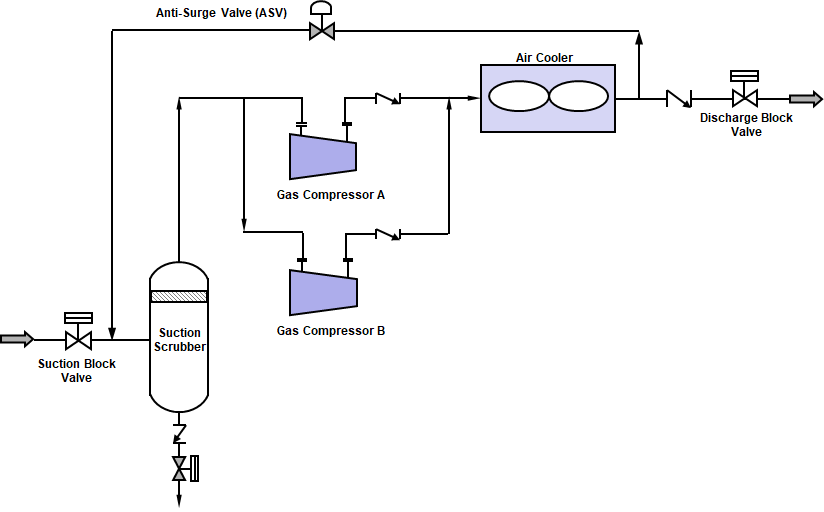
The corrections that are required to be made are as follows,
- IDENTICAL COMPRESSOR OPERATION: Having parallel compressors would mean both of them should run identically at the same speed & similar process conditions.
- LOAD SHARING SCHEME: Parallel compressor operation would mean installing a Load Sharing scheme where each Variable Frequency Drive’s (VFD) speed controller would take a set point from a master pressure controller (MPC) that is installed on the suction header & alters the compressor speed accordingly. This way, deviation between compressor speeds is reduced.
- INSTABILITY DURING PARALLEL OPERATION: With a single anti surge line for both parallel compressors, during gas recycling, both compressors are going to face an imbalance even if one compressor trips. This is true even with a spare compressor (if available) starting up. So each compressor must have its own anti-surge line whether its a series or parallel arrangement. In case of series arrangement, each compressor's Anti-surge lines can be compensated by an overall pressure balancing line.
- INDIVIDUAL SUCTION SCRUBBERS: Each compressor has to have its own scrubber, instead of having a common suction scrubber. Individual smaller suction scrubbers sized for their respective compressor flow might add up to the cost & take up extra installation space compared to a single suction scrubber. However this gives more control over each compressor by avoiding any propagation of flow disturbances between compressors.
- AIR COOLER FAILURE: With only a single common air cooler & its failure, there will be plenty of hot gas entering into the downstream equipment (e.g., export pipeline). If this compressor discharge temperature is above the downstream equipment design temperature, then you are going to potentially see thermal damage. With individual coolers, even if one cooler fails, the colder gas from the other parallel compressor can dilute & lower the export pipeline temperatures.
- RECYCLE CONDITIONS: During recycle conditions, if the common single air cooler fails, You will again have plenty of hot gas entering your compressor which will overheat and also trip the compressor.
- FLOW DISTRIBUTION PROBLEMS: With only a single common anti-surge line, chances are high that the flow distribution would not be equally distributed between compressors when the pipe routing is not exactly similar & also because both compressor curves will not be exactly the same. This during startup, Normal Shutdown (NS)D or Emergency Shutdown (ESD) might create conditions for a surge.
Vijay Sarathy holds a Master’s Degree in Chemical Engineering from Birla Institute of Technology & Science (BITS), Pilani, India and is a Chartered Engineer from the Institution of Chemical Engineers, UK. His expertise over 16 years of professional experience covers Front End Engineering, Process Dynamic Simulation and Subsea/Onshore pipeline flow assurance in the Oil and Gas industry. Vijay has worked as an Upstream Process Engineer with major conglomerates of General Electric, ENI Saipem and Shell.