Quality control is an essential aspect of any organization's operations, regardless of its size or industry. It ensures that products and services meet or exceed customer expectations, thereby enhancing customer satisfaction and loyalty. To achieve and maintain high-quality standards, many organizations turn to established methodologies and frameworks, one of the most widely recognized being the PDCA (Plan-Do-Check-Act) cycle.
This versatile framework is a cornerstone of quality control, empowering organizations to continuously improve their processes, products, and services.
In this article, we'll explore the PDCA cycle in quality control, its components, and its role in driving excellence within an organization.
Understanding the PDCA Cycle
The PDCA cycle, often referred to as the Deming Cycle or the Shewhart Cycle, was developed by Walter A. Shewhart and popularized by W. Edwards Deming, two prominent figures in the world of quality management. This four-step cycle serves as a systematic approach for process improvement, problem-solving, and overall quality control.
- Plan (P): The first step involves identifying a problem, setting objectives, and creating a plan to achieve those objectives. During this phase, organizations determine what needs improvement, set goals, and develop a strategy to reach those goals. This planning stage serves as the foundation for the entire PDCA cycle.
- Do (D): The second step is about implementing the plan. It involves executing the plan on a small scale or in a controlled environment to test its effectiveness. This stage helps organizations gather data, identify potential issues, and assess the practicality of their proposed improvements.
- Check (C): In the third step, organizations assess the results of the "Do" stage by collecting and analyzing data. This evaluation helps determine if the plan is working as expected, if the goals are being met, and if any adjustments are needed. It's a critical phase for understanding the impact of the changes made.
- Act (A): The fourth and final step involves taking appropriate actions based on the results of the "Check" phase. If the plan has been successful, organizations standardize the changes and integrate them into their processes. If the plan didn't yield the expected results, they revise the plan and repeat the cycle until the desired outcomes are achieved.
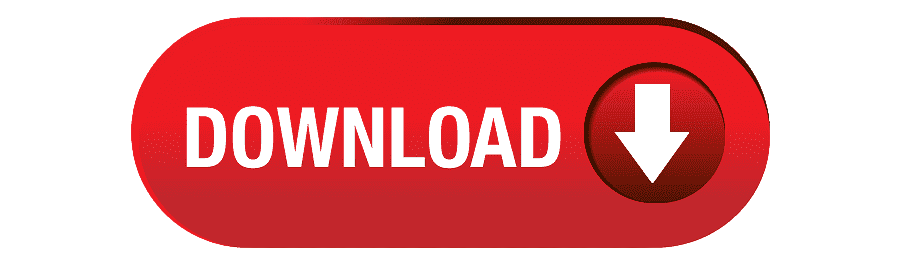
Key Benefits of the PDCA Cycle in Quality Control
The PDCA cycle offers several significant advantages for organizations seeking to maintain and improve their quality control processes:
- Systematic Improvement: The PDCA cycle provides a structured approach to solving problems and making improvements. It helps organizations avoid knee-jerk reactions and instead encourages methodical problem-solving.
- Data-Driven Decisions: Each phase of the PDCA cycle relies on data collection and analysis, making it easier to make informed decisions and track progress.
- Continuous Improvement: PDCA is inherently designed for continuous improvement. By repeatedly cycling through the process, organizations can continuously refine their processes and enhance their quality standards.
- Waste Reduction: Through PDCA, organizations can identify and eliminate inefficiencies, reducing waste and improving resource utilization.
- Risk Mitigation: The PDCA cycle allows organizations to test and assess changes on a small scale before implementing them organization-wide, reducing the risk of major disruptions or failures.
- Cultivating a Culture of Quality: Using the PDCA cycle promotes a culture of quality within the organization, as employees become accustomed to identifying and addressing issues as they arise.
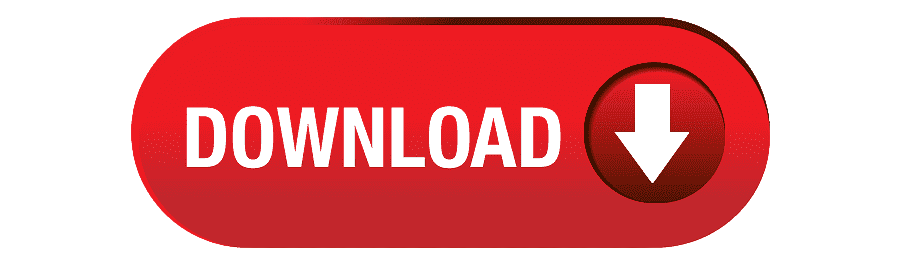
Applications of PDCA in Different Sectors
The PDCA cycle is a versatile framework that finds applications in various industries and sectors. It's widely used in manufacturing, healthcare, software development, and many other fields. Here are a few examples of how PDCA is applied in different sectors:
- Manufacturing: In manufacturing, PDCA is used to optimize production processes, reduce defects, and enhance product quality. It can lead to improved machinery, streamlined workflows, and increased overall efficiency.
- Healthcare: In healthcare, the PDCA cycle can help enhance patient care, reduce medical errors, and improve hospital procedures. It's used to identify and eliminate bottlenecks, improve patient outcomes, and enhance the overall quality of care.
- Software Development: In the realm of software development, PDCA can lead to better software products with fewer bugs. It's employed to enhance development and testing processes, resulting in higher-quality software applications.
- Service Industry: In the service industry, PDCA can lead to improved customer service, streamlined operations, and higher levels of customer satisfaction. It's used to identify areas where service can be improved and to implement changes that enhance the customer experience.
Challenges in Implementing PDCA
While the PDCA cycle is a powerful tool for quality control and continuous improvement, its successful implementation can face challenges. Some of these challenges include:
- Resistance to Change: Employees and management may resist changes to existing processes, even when those changes are clearly beneficial. Effective communication and change management strategies are essential to address this challenge.
- Data Collection and Analysis: Collecting and analyzing relevant data can be time-consuming and complex. Organizations must invest in the right data collection tools and analytics capabilities.
- Resource Constraints: Implementing the PDCA cycle may require additional resources, such as time and personnel. Organizations need to balance these demands with their existing commitments.
- Lack of Training: If employees are not adequately trained in the PDCA methodology, the cycle may not be as effective as desired. Training and ongoing support are critical for success.
Conclusion
The PDCA cycle in quality control is a robust framework that empowers organizations to continuously improve their processes, products, and services. By following the Plan-Do-Check-Act cycle, organizations can systematically identify and resolve issues, reduce waste, and cultivate a culture of quality.
While the implementation of PDCA may pose challenges, the benefits of improved quality, increased customer satisfaction, and enhanced operational efficiency make it a valuable tool for any organization committed to excellence in their industry.